Pumps are indispensable tools in many industries, especially in the chemical industry. A chemical pump is a device that moves fluids, such as chemicals, from one point to another. It is used to transfer and meter liquids, gases, or slurries. There are different types of chemical pumps, including centrifugal pumps, diaphragm pumps, piston pumps, and peristaltic pumps.
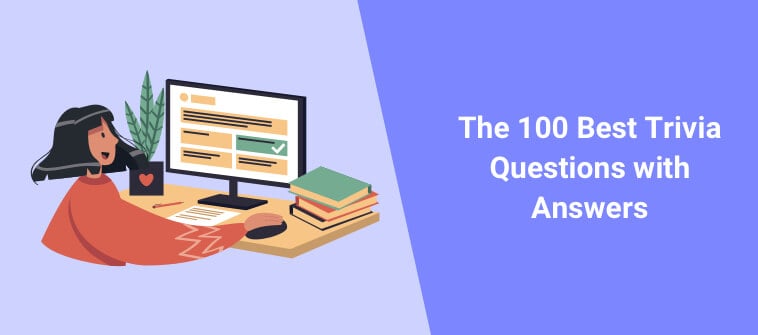
Chemical pumps are essential in the chemical industry because they facilitate the transport and handling of dangerous, toxic, or corrosive substances. These pumps are designed to be chemical-resistant and have specific features that make them suitable for chemical applications. In this blog, we will discuss some of the features of chemical pumps and their applications.
Features of Chemical Pumps
1. Corrosion Resistance
Chemical pumps are made of materials that are resistant to corrosion. These materials include stainless steel, alloy, ceramic, and plastic. This type of pump is essential in the chemical industry because most chemicals are corrosive, which makes ordinary pumps unsuitable for chemical applications.
2. Seal-less Design
Chemical pumps have a seal-less design, which means they do not have shaft seals that can cause leaks or contaminate the fluid being pumped. This feature reduces maintenance costs and ensures the purity of the pumped fluid.
3. Self-Priming
Chemical pumps have a self-priming feature, which means they can pump liquids without the need for external priming. This feature is essential in situations where the pump is located above the liquid level or when the fluid being pumped is viscous or mixed with air.
4. High Temperature and Pressure Resistance
Chemical pumps are designed to handle high temperatures and pressures, which makes them suitable for high-pressure applications in the chemical industry. The pump's resistance to high temperatures and pressures ensures that it does not fail when transporting dangerous or volatile chemicals.
Applications of Chemical Pumps
1. Chemical Transfer
Chemical pumps are used for the transfer of liquids and gases between different containers, such as storage tanks and processing equipment. Chemical pumps are essential in the chemical industry because they facilitate the transfer of dangerous or toxic chemicals safely.
2. Water Treatment
Chemical pumps are used in water treatment plants to pump chemicals such as chlorine, fluoride, and ozone to disinfect and treat water. These pumps are designed to handle corrosive chemicals and ensure that they are delivered accurately and efficiently.
3. Pharmaceutical Industry
Chemical pumps are used in the pharmaceutical industry to transport chemicals used in the manufacturing of drugs. These pumps are designed to meet the strict regulatory requirements for pharmaceutical production, such as cleanroom environments, to ensure the purity of the drugs being manufactured.
Conclusion
Chemical pumps are critical tools in the chemical industry, and they facilitate the safe transport and handling of dangerous or corrosive chemicals. With their corrosion-resistant materials, seal-less design, self-priming feature, and high-temperature and pressure resistance, chemical pumps are the preferred choice for chemical applications. Additionally, their applications are diverse, from chemical transfer to water treatment and pharmaceutical production. To ensure the safe and efficient handling of chemicals, it is essential to use the right chemical pump for the application.